Jean Hardy* spoke to Ruud Dorscheidt** and Ibn Delaet*** at Sibelco on the company’s glass recycling projects, as well as its strategies for fostering greater collaboration across the industry.
In 1872, workers digging Belgium’s Antwerp to Liège Canal uncovered a vast deposit of high-quality silica sand. This led to the formation of Sablières et Carrières Réunies (Combined Sand Pits and Quarries), today known as Sibelco, which began to supply sand to glass and ceramics manufacturers.
Over the past 150 years, Sibelco has grown into a global material solutions company, sourcing, transforming and delivering speciality industrial minerals globally, with operations spanning more than 30 countries.
Now Sibelco has created a strategic roadmap for growth, called ‘Build 2030’. The pillars of this strategy are as follows:
- Global leadership in three core sectors: industrial silica, high-purity quartz and recycled glass.
- Regional leadership in selected other silicate materials, including olivine, feldspathics and clays.
- Strong support to its customers, such as glass producers, in their decarbonisation journey.
- Continued support and development of Sibelco’s employees, who play a central role in the company’s operations.
Sibelco entered the glass recycling business in the early 2000’s, with the acquisition of local recycling companies Pate in France and Minerale in Belgium.
Now, the company has 23 recycling plants active in six European countries: Italy, the United Kingdom, Poland and Estonia, in addition to Belgium and France.
Having built a strong recycling presence in Europe, Sibelco tackled the American market in 2024 with its acquisition of Strategic Materials. The company is North America’s largest glass recycler, with plants in the USA, Canada and Mexico.
The acquisition placed Sibelco as a global leader in glass recycling with 60 production sites, 5 million tons of cullet treated per year with more than 1,000 collaborators.
Glass recycling
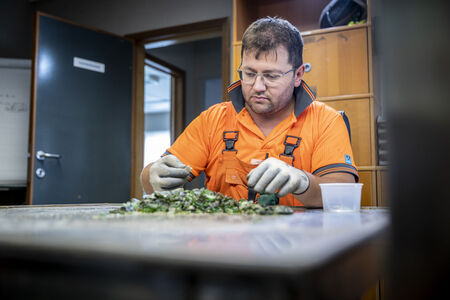
Glass recycling has many benefits, including: more ecological glass, as cullet uses 25% less melting energy, which means less CO2 emissions; less waste, ideally this would mean no more landfill; and less use of natural resources, also known as primary materials.
The recycling of glass containers used for packaging such as bottle and jars has been well-established in many countries, but the recycling rate for flat glass is still low.
This is due to two main reasons: higher requirements regarding glass purity and homogeneity; and the recycling of windows, doors and façades is more complex than glass packaging.
However, both flat glass producers and glass recyclers have taken up the task and are developing some promising processes.
Glass recycling projects
Sibelco is currently working on several recycling projects, including the three outlined below.
High 5 Glass
The first one is the High 5 Glass Recycling facility, based in Antwerp’s harbour in Belgium, which handles 300,000 tons of cullet on a yearly basis.
- Input: includes high end bottle bank collection from Belgium, the Netherlands and the north of France, as well as Material Recycling Facility (MRF) material coming from the United Kingdom by vessel.
- Output: glass in the colours flint, green, amber and dead-leaf. Due to its low chromium content and redox state, dead-leaf cullet is used to produce amber glass without impacting the colour specifics.
- Logistics: multimodal connection (road to the Albert canal), allowing access to container glass producers located mainly in Germany and in the Netherlands.
Chanel N°5
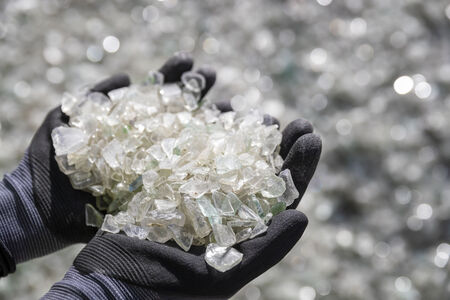
The second project serves as an example of a successful collaboration between glass producers and recyclers.
It also solved a problem for which it was thought that there was no solution: the high iron content in post-consumer glass waste affecting the transparency and shine of the luxury perfume bottles.
When Chanel asked Pochet Du Courval to create a limited-edition bottle using recycled glass to mark the 100th anniversary of Chanel N°5, Sibelco was called in to help.
Working in partnership with Pochet Du Courval, Sibelco’s glass recycling team began running tests at its Reims plant in France. The team also worked closely with a company that supplies optical sorting equipment.
Within a year, the project’s partners had found a way to produce low-iron cullet (Fe2O3 < 500 ppm) using specially developed optical sorting technology.
To enhance the performance of the new cullet, Sibelco low-iron dolomite and Alumina Tri-Hydroxide (ATH) were also added to the glass batch.
A mixed solution of recycled glass and fresh raw materials requires an in-depth knowledge of material melting, which only a few companies, such as Sibelco, possess.
Glassy carbon
The final project involves one of the outputs from the recycling process – “glassy carbon”. It is used as an active component in glassmaking, due to its effect on the redox balance inside a glass furnace.
With knowledge of the characteristics of the glassy carbon, the correct amount of material to add can be determined and will yield a consistent result.
This will allow glass producers to replace natural carbon with glassy carbon, and increase the total amount of recycled content.
Collaboration
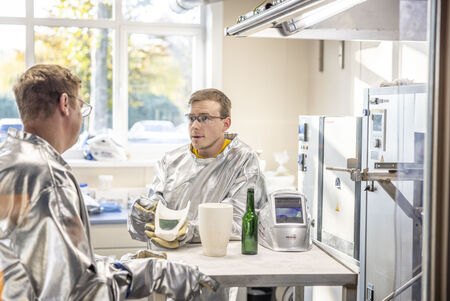
One of Sibelco’s oldest factories is in Belgium, located in Dessel, Kempen, near the site where the first silica sand deposit was discovered.
It contains the Technology and Innovation Glass Lab (see right), where eight specialists perform physical, chemical, and mineralogical analyses using modern equipment: viscometers, furnaces, polariscopes, spectrophotometers, and more.
Ruud Dorscheidt, Director of Product and Waste Management, said: “The laboratory is important, it is where we test our mined products at different stages of their processing. But this is also where we carry out various tests and experiments, in close collaboration with our customers.
“We are no longer in a binary logic, i.e. raw material suppliers on the one hand and customers on the other side – including glass producers.
“We are resolutely in a joint approach, bringing together suppliers and customers. Moreover, we often involve third-party service providers, such as equipment suppliers, in this approach.”
Mr Dorscheidt and Ibn Delaet, from Group Communications, emphasised the need for active collaboration between glass producers and recyclers.
They explained how a structural change implemented by Sibelco four years ago has allowed for greater collaboration, as well as bringing the company closer to its customers.
Previously, Sibelco operated in a top-down manner, where decisions were made by Business Units at a global level and passed down. Now, Sibelco has shifted to a bottom-up approach, allowing local teams to have more autonomy in management and decision-making.
The new structure is organised into approximately 40 locally formed clusters. These clusters report to higher levels, i.e. sub-regions and continents, but act as decentralised, entrepreneurial units, while respecting global governance framework.
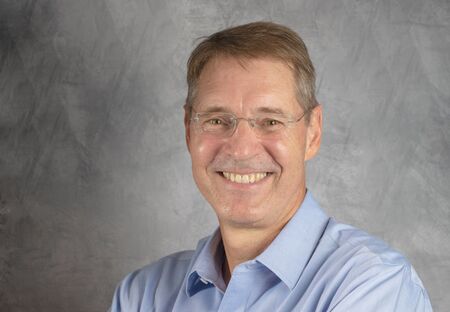
Sibelco CEO Hilmar Rode (see above) said: “At Sibelco, we are committed to becoming a global leader in industrial silica, high purity quartz and glass recycling. Embracing circularity and sustainability is in our mission and purpose: ‘material solutions advancing life’.
“We as Sibelco are happy to actively collaborate with the glass producers to enhance product performance via our advanced glass recycling solutions and through strong partnerships, sharing our expertise and bring innovation, we always strive to deliver impactful results that benefit both the glass industry and the planet.”
*Freelance correspondent, Glass International, Managing Partner of JH Finance & Glass, Louvain-la-Neuve, Belgium, https://www.jhfinaglass.eu/
**Director of Product and Waste Management, ***Group Communications, Sibelco, Antwerp, Belgium, https://www.sibelco.com/en
Credentials : See the original article
LinkedIn: @Glass International
Instagram: @glassinternationalnews
X: @Glass_Int